In this blog article you will learn learn curing of concrete. I will also describe curing period, concrete curing time chart, curing methods and other related information.
Concrete is a composite material consisting of cement, sand, and water in appropriate proportions. The chemical interaction between cement and water help to binds the aggregate. Wet concrete will be plastic so that it can be molded to any desired shape and compacted to form a dense mass.
Concrete must be placed in a position before it starts losing its plasticity. The time when concrete completely lost its plasticity and became hard is called the final setting time of concrete.
Table of Contents
What Is Curing Of Concrete?
Curing plays a crucial role in concrete strength development and durability. After adding water to the mixed concrete (Cement, Sand & Aggregate), the exothermic reaction (hydration) took place, which assists the concrete to harden. Hardening of concrete is not a quick process and continues for a longer period, which needs more amount of water for processing hydration. Hence, the concrete is kept moist until the hydration reaction in concrete completes. This process is known as the curing of concrete.
In other words,
Concrete Curing is the process in which the concrete is kept moist to prevent it from loss of moisture due to atmospheric temperature and hydration reaction.
Purpose Of Concrete Curing
The reaction between cement and water is known as hydration. It is an exothermic reaction (the reaction which discharges heat).
After adding water to the concrete mix, hydration begins, which makes the concrete dry out rapidly due to an exothermic reaction that discharges heat. To complete the hydration process, concrete is kept moist to achieve the maximum strength of concrete as soon as possible.
Concrete Curing Procedure:
Draining water on the surface of concrete cures the concrete. A water cooler than 50C is not appropriate for curing concrete. As the hydration reaction in concrete kick out heat and keep the concrete warm, Using cold water less than 50C on concrete may lead to cracking and failure. Alternate drying and wetting on the concrete surface causes volumetric changes in concrete and finally leads to cracking.
Curing Period Of Concrete
The minimum period for curing concrete to achieve maximum strength is 28 Days.
For a clear knowing, check out the concrete curing time chart.
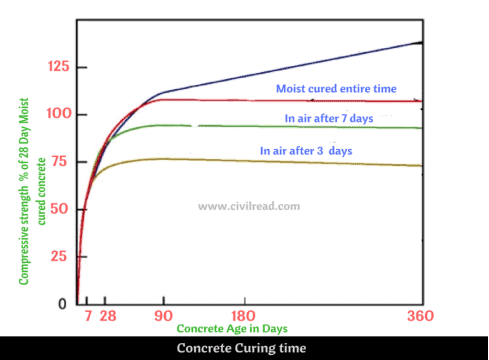
From the above image, it is understood that concrete achieved 50% of its design strength when it was cured for 3-7 Days. 75% of Compressive strength was attained in 14 days. 90% of Concrete design strength was attained in 28 days. Thus it is clear as time increases the concrete strength increased.
Minimum Curing Time For Cement Concrete:
The early strength of concrete is most crucial, and it is accountable for the ultimate strength of concrete. We should do correct curing by considering the environmental conditions, type of structural members, atmospheric temperature. Maintaining the right temperature also plays a crucial role in concrete as mentioned, it should not be colder than 50C. Concrete is kept moist for a minimum of 28 days. At present, due to lack of time, curing can be attained by following modern techniques in 14-20 Days. However, it is always recommended to keep concrete moist for at least 14 days.
Concrete should not be cured in less than 7 days for ordinary Portland Cement (OPC), & it must be at least 10 days for concrete with mineral admixtures or blended cement. In case of hot weather and arid temperature circumstances, the curing should not be less than 10 days for OPC and 14 days for concrete with blended cement & mineral admixtures.
The curing time or period of concrete depends on factors as follows:
- Specific Strength of concrete.
- Different Grades of concrete.
- Atmospheric conditions like temperature, humidity, etc.
- Size and shape of the concrete structure
Concrete Curing Methods:
Below are the most important methods which are prominently used all over the world.
1. Ponding:
This technique is used for floor slabs. The concrete surface is divided into small ponds, and these ponds are occupied with water continuously for 14 days.
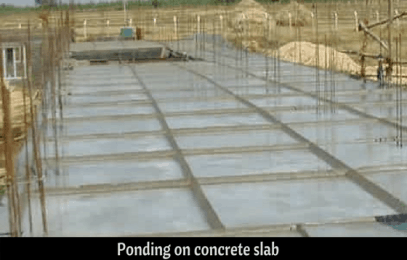
2. Wet coverings:
This technique is used for columns, footings, and the bottom surface of slabs, where ponding is not possible. Impermeable coverings such as gunny bags or hessian are needed to cover the concrete; these membranes are sprayed with water to keep the concrete moist.
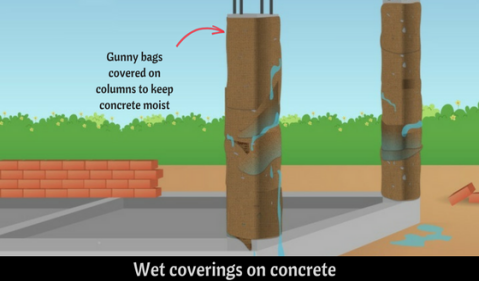
3. Membrane Curing of Concrete:
Ponding is not appropriate at places where atmospheric temperatures are high. Water gets evaporated owing to excessive heat. Membrane curing is adopted to forestall the loss of water content due to atmospheric temperature from concrete.
Membrane curing assists seal off by forming an impermeable layer on the concrete surface, which eventually oppose evaporation. This process is mostly performed by brushing or spraying the curing compound on the concrete surface.
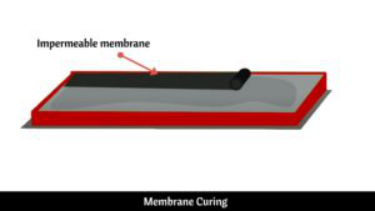
Different curing compounds are acquirable to achieve the membrane curing out of them, below four methods are essential and widely used.
(a) Synthetic Resin Curing Compound:
Synthetic resin is a compound that forms as an impermeable membrane on a concrete surface to defy the water evaporation from concrete.
To continue with further plastering, the synthetic resin membrane can be easily removed by spraying the hot water on the concrete surface. Thus it is appropriate at areas where subsequent treatment is applied to the concrete.
(b) Acrylic Curing Compound:
Acrylic Curing compound is a polymer-based curing compound acquired from the polymers of Acrylic acid.
The best part of the Acrylic-based curing compound is there is no necessity to remove this compound for plastering. Acrylic assists to attain excellent adhesion to plastering.
(c) Wax Curing Compound:
Wax curing has the same properties as synthetic resin. The use of wax on the surfaces to be painted or tiled is not advisable because wax hampers the adhesion between the surface and plastering or tiling.
(d) Chlorinated Rubber Curing Compound:
Chlorinated rubber forms a thick membrane on the concrete surface when laid. The use of chlorinated rubber-based curing compound seals the concrete effectively with no minute pores left. But the age of chlorinated rubber is very less, and it cannot stay for a longer period of time.
4. Steam Curing of Concrete:
This process is adopted at a Precast concrete plant where the concrete members are mass-produced. Steam has heat moisture in it, and it is sprayed on the concrete surface to keep concrete moisture and also enhance the concrete temperature, which eventually quickens the pace of hardening concrete.
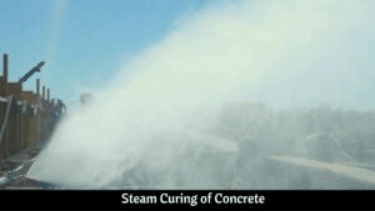
5. Curing of Concrete by Infrared Radiation:
This technique is adopted in cold climatic regions. In this process, infrared radiation is applied to the concrete, increasing the initial temperature, which increases the strength of concrete. This is the most effective technique than steam curing, as raising the initial temperature in concrete does not reduce the ultimate strength of concrete. This method is used for the hollow concrete members where the heaters are placed in concrete members which emit a temperature of 900 degrees.
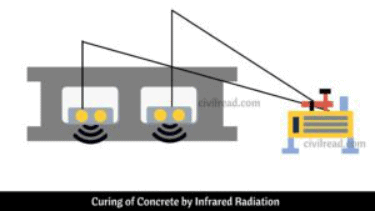
6. Curing of concrete by an Electric Current:
In this technique, the concrete is cured by passing an alternating current to it. Two plates, one at the top and another at the bottom of the concrete surface, works as an electrode, and then the alternating current is passed to them. 30V or 60V of potential difference maintained among these two electrodes. The curing achieved by concrete at 28 days can be achieved within three days by performing this technique.
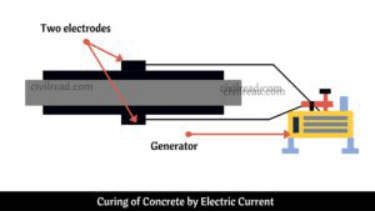
Conclusion
It was all about the concrete cure, its methods and the timing of the cure. I hope you like it. Thanks for reading my article.
Faq
Self-curing concrete is concrete that can cure without the need for external water curing methods.
Self-curing concrete contains chemicals that react with the water and cement to create a continuous supply of moisture, which helps to keep the concrete hydrated and promote curing.
Using self-curing concrete can reduce the need for external water curing methods, result in a more consistent curing process, and lead to a stronger and more durable final product.
The ideal temperature range for curing concrete is between 10°C to 32°C.
Curing concrete at too high or too low temperatures can result in reduced strength and durability, as well as cracking and brittleness.